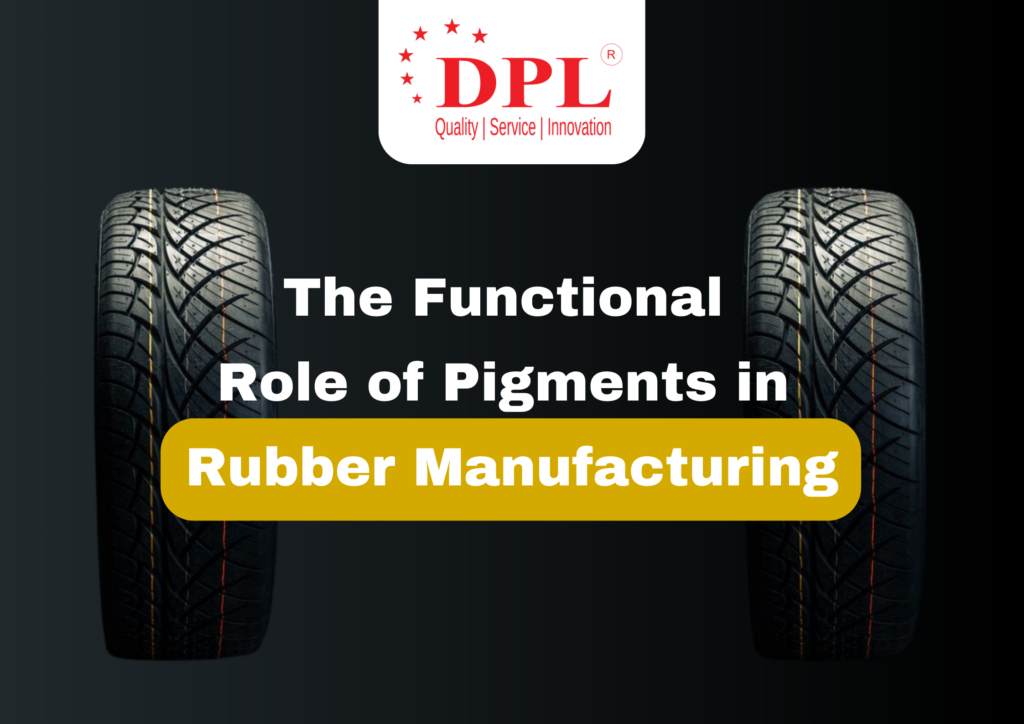
In the rubber manufacturing industry, pigments play an essential role in more than just adding colour. As a manufacturer, you know that rubber products are expected to meet high standards of durability, flexibility, and performance. However, what many may not realize is how important pigments are in achieving those qualities. Beyond the obvious visual appeal, pigments contribute to the physical properties and functionality of rubber, making them a critical ingredient in the production process.
Let’s explore how pigments go beyond colour and influence the overall performance of rubber products.
Why Pigments Matter in Rubber Manufacturing
As a manufacturer, you’re constantly balancing the demands for aesthetics, functionality, and cost-effectiveness. Pigments in rubber manufacturing address all three of these concerns in various ways:
Colour Consistency
While colour may seem like a cosmetic feature, it’s a vital aspect of brand identity and consumer preference. Using high-quality pigments ensures that your rubber products maintain consistent, vibrant colours that won’t fade easily, even under extreme conditions. Whether you’re producing automotive parts, footwear, or industrial gaskets, reliable colour is a must for maintaining product appeal.
UV Resistance
Many rubber products are exposed to outdoor environments, where they face the damaging effects of UV radiation. Pigments, particularly those designed with UV-stabilizing properties, help protect the rubber from degradation caused by sunlight. By incorporating the right pigments, you can extend the life of your products, reducing the likelihood of cracking, fading, or becoming brittle over time.
Heat Resistance
In applications where rubber products are exposed to high temperatures, pigments contribute to thermal stability. Certain pigments can reflect heat, helping the rubber material resist degradation. This is especially important for automotive or industrial products that must endure significant heat without losing their structural integrity.
The Science Behind Pigments in Rubber
Pigments in rubber manufacturing aren’t just about adding colour—they’re carefully selected for their chemical properties and how they interact with the rubber matrix. Pigments can be organic or inorganic, with each type offering distinct benefits:
- Inorganic Pigments: These are often preferred for their durability and resistance to heat and light. They’re made from minerals such as titanium dioxide or iron oxide. Inorganic pigments are excellent for outdoor rubber products that must withstand harsh environmental conditions. For instance, titanium dioxide offers excellent whiteness and opacity, while iron oxides provide a range of earthy tones and high durability.
- Organic Pigments: These pigments, derived from carbon-based molecules, offer brighter and more vibrant colours than their inorganic counterparts. However, they are often less stable in terms of heat and light resistance. Organic pigments are frequently used in applications where vibrant colours are needed, and the products aren’t exposed to extreme conditions, such as indoor footwear or toys.
Improving Mechanical Properties
Pigments can also enhance the mechanical properties of rubber. For example, some pigments act as fillers, improving the overall strength and durability of the rubber product. In fact, certain pigments, like carbon black, do more than just colour the rubber black—they significantly enhance its tensile strength, abrasion resistance, and overall durability.
If your product requires additional durability for heavy use or high-stress applications, selecting the right pigments can improve its performance while maintaining the desired aesthetic.
Achieving Uniform Dispersion
One of the key challenges in rubber manufacturing is achieving uniform dispersion of pigments throughout the material. Pigment particles must be evenly distributed to ensure consistent colour and performance across the product. Poor dispersion can lead to issues such as weak spots, uneven colouring, or reduced durability.
As a manufacturer, it’s essential to work with high-quality pigments that are designed to blend well with the rubber matrix. Proper dispersion also ensures that the mechanical and protective benefits of the pigments, such as UV resistance or heat stability, are distributed evenly across the rubber product, giving it uniform performance characteristics.
Pigments and Cost Efficiency
In addition to enhancing the physical properties of rubber, pigments can also help reduce manufacturing costs. Certain pigments, especially those that function as fillers, can lower the overall cost of raw materials by reducing the amount of expensive polymers needed. For example, carbon black, which is widely used in rubber manufacturing, acts as both a pigment and a reinforcing agent, reducing the need for more costly rubber ingredients while improving product performance.
By choosing the right pigments, you can achieve a balance between cost savings and product quality, ensuring that your rubber products meet performance expectations without exceeding budget constraints.
Meeting Consumer Demands for Sustainability
Sustainability is a growing concern in every industry, and rubber manufacturing is no exception. Many consumers today are looking for eco-friendly products that align with their environmental values. The pigments you choose can play a role in how sustainable your products are perceived.
Inorganic pigments, such as those based on natural minerals, are often more environmentally friendly than synthetic alternatives. By incorporating these into your products, you can appeal to consumers who prioritize sustainability while maintaining high standards of quality and performance.
Versatility Across Applications
Whether you’re producing industrial seals, automotive tires, consumer goods, or medical products, pigments play a crucial role in adapting rubber to its intended use. Each application has specific requirements, from flexibility to resistance to harsh chemicals or weather conditions. The pigments you select can be tailored to meet those needs, giving your products the performance boost they require for their respective markets.
For example:
- Automotive Tires: Carbon black, a widely used pigment, not only enhances the tire’s strength but also offers superior heat dissipation, making it perfect for tires that endure long-distance travel and heavy loads.
- Medical Products: In the medical industry, pigments used in rubber must meet stringent safety and quality standards. Pigments that provide non-toxic, durable, and easily sterilizable rubber products are essential for medical-grade rubber used in gloves, tubing, and seals.
- Consumer Footwear: Pigments for rubber soles must provide vibrant colours while enhancing the slip resistance and flexibility of the shoe. Pigments with these dual functions make a significant difference in product appeal and safety.
Final Thoughts
As a rubber manufacturer, you understand the importance of every component in your products, and pigments are no exception. The pigments you choose not only define the appearance of your rubber products but also contribute to their strength, durability, and overall performance.
By selecting the right pigments—whether for UV protection, heat resistance, or mechanical reinforcement—you can create products that meet the high expectations of your customers. The functional role of pigments in rubber manufacturing is more than just skin deep. They are an integral part of producing high-quality, reliable, and cost-effective rubber products that stand the test of time.
Investing in the right pigments means investing in the long-term success of your rubber products, ensuring they meet both aesthetic and functional needs in an increasingly demanding marketplace.