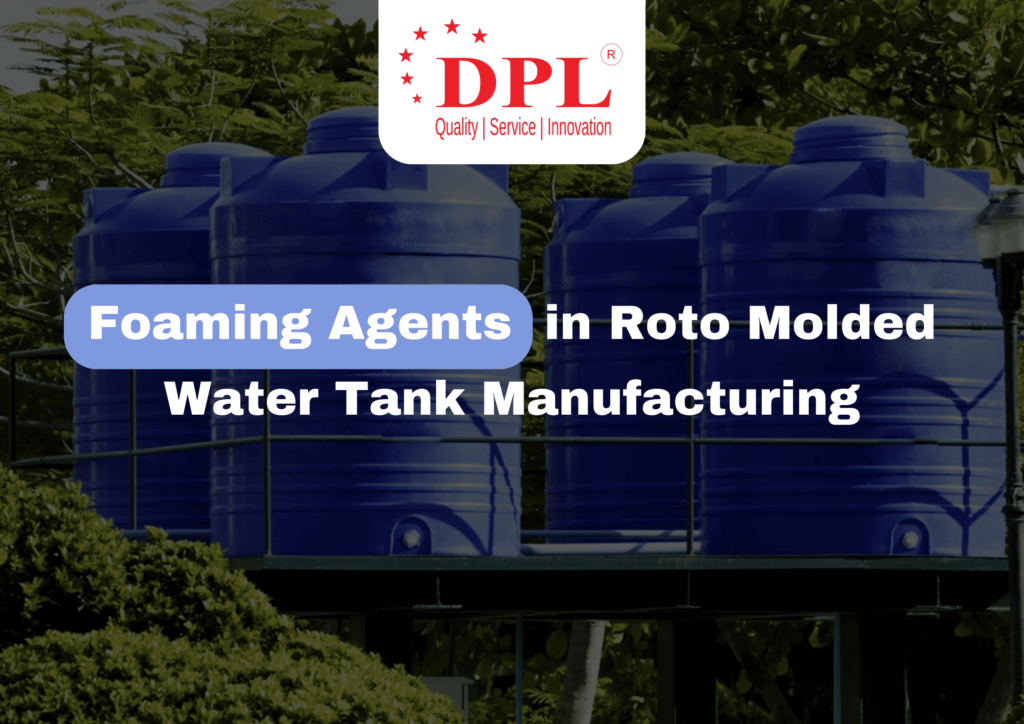
Rotational moulding (roto moulding) has become a preferred manufacturing process for producing high-quality, lightweight, and durable water tanks. A critical component of this process is the use of foaming agents, which significantly enhance the structural properties of the final product while optimising manufacturing efficiency. These agents create a foamed structure within the material, resulting in water tanks that are both strong and lightweight.
As a leading ADCL foaming agent supplier, DPL Group is committed to providing advanced solutions that cater to the evolving demands of the water tank manufacturing industry. This article delves into the role of foaming agents in roto-molded water tank production and highlights their benefits, applications, and future trends.
What Are Roto-Molded Water Tanks?
Roto-moulded water tanks are produced using rotational moulding, a versatile manufacturing technique. This process involves heating a polymer resin in a mould that rotates along multiple axes, ensuring uniform distribution of material and eliminating seams or weak points. The addition of foaming agents during this process further enhances the tank’s properties.
Role of Foaming Agents in Roto-Molding
Foaming agents are chemical additives used to introduce a cellular structure within the polymer matrix during the moulding process. This creates a foamed layer that improves the tank’s overall performance. The key contributions of foaming agents include:
Lightweight Structure
Foaming agents reduce the density of the polymer material by creating a cellular structure. This lightweight design ensures easy handling and transportation without compromising strength.
Enhanced Insulation
The foamed structure provides superior thermal insulation, maintaining water temperature within the tank and reducing external heat impact.
Improved Strength-to-Weight Ratio
Tanks produced with foaming agents exhibit an excellent strength-to-weight ratio, making them durable and resistant to mechanical stress.
Cost Efficiency
By reducing the overall material consumption, foaming agents lower production costs while maintaining high-quality standards.
Eco-Friendly Manufacturing
Foaming agents contribute to sustainable production by minimising material usage and energy consumption, aligning with global environmental goals.
Types of Foaming Agents Used in Roto-Molding
Foaming agents used in rotational moulding can be categorised into two types:
- Chemical Foaming Agents (CFAs): These agents decompose at elevated temperatures, releasing gases such as nitrogen or carbon dioxide. Popular CFAs like ADCL foaming agents are known for their efficiency and compatibility with various polymers.
- Physical Foaming Agents (PFAs): PFAs use physical methods, such as gas injection, to create a foamed structure. While effective, they are less commonly used in roto moulding due to equipment complexity.
Benefits of Using ADCL Foaming Agents in Water Tank Manufacturing
ADCL foaming agents are specifically engineered for rotational moulding applications, offering unmatched benefits:
- Uniform Cellular Structure: ADCL foaming agents ensure consistent cell formation, resulting in uniform thickness and strength throughout the tank.
- High Thermal Stability: These agents perform well under the high-temperature conditions of rotational moulding, ensuring reliability and efficiency.
- Customisable Density: ADCL foaming agents allow manufacturers to control the density of the final product, catering to specific application requirements.
- Compatibility: Compatible with a wide range of polymers, including polyethene and polypropylene, these agents offer versatility for various tank designs.
- Cost-Effective Solutions: With ADCL foaming agents, manufacturers can achieve significant cost savings without compromising on quality or durability.
- Enhanced Impact Resistance: ADCL foaming agents contribute to the production of tanks with improved shock absorption and impact resistance, making them suitable for harsh environments and rough handling.
- Reduced Material Usage: By enabling the creation of a foamed structure, ADCL foaming agents minimize raw material consumption, promoting resource efficiency and reducing production waste.
- Lightweight Construction: Tanks manufactured with DCL foaming agents are significantly lighter, making them easier to transport and install without compromising structural integrity.
- Improved Insulation Properties: The cellular structure formed by ADCL foaming agents provides superior thermal insulation, helping maintain the temperature of stored water and protecting it from external heat or cold.
Future Trends in Roto-Molded Water Tank Manufacturing
The demand for high-performance water tanks continues to grow, driving innovation in roto-molding techniques and materials. Some emerging trends include:
- Eco-Friendly Foaming Agents: Manufacturers are exploring biodegradable and low-emission foaming agents to meet environmental regulations.
- Smart Tanks: Incorporating IoT-enabled sensors in roto-moulded tanks for real-time monitoring of water levels, quality, and usage patterns.
- Advanced Polymer Blends: Development of new polymer blends with enhanced strength and flexibility to improve tank performance.
- Automation in Manufacturing: Integrating advanced robotics and AI to streamline the roto-moulding process, ensuring consistency and efficiency.
Final Thoughts
Foaming agents are revolutionising the roto-moulding process, enabling the production of lightweight, durable, and efficient water tanks. Their ability to enhance thermal insulation, reduce material costs, and improve strength-to-weight ratios makes them indispensable in water tank manufacturing.
As a trusted ADCL foaming agent supplier, DPL Group provides high-quality solutions tailored to the needs of the rotational moulding industry. Our foaming agents are designed to optimize manufacturing efficiency while ensuring the durability and performance of your water tanks.
Contact us today to learn how our DCL foaming agents can transform your water tank manufacturing process!