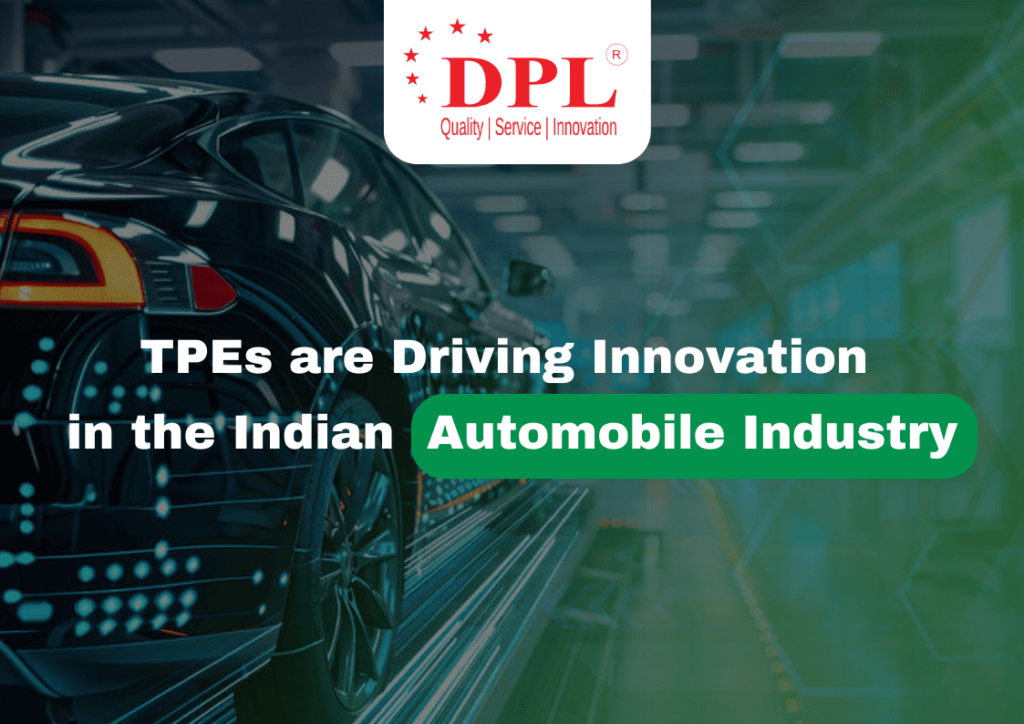
In recent years, the Indian automobile industry has witnessed remarkable growth and transformation. With increasing demands for efficiency, sustainability, and comfort, manufacturers are constantly seeking advanced materials that can meet the evolving requirements of vehicles. Among these materials, Thermoplastic Elastomers (TPEs) have emerged as a game changer, driving innovation and reshaping automobile manufacturing in India.
This article explores how TPEs are revolutionising the Indian automobile sector, their applications, benefits, and why DPL Group is at the forefront of this material revolution.
Understanding Thermoplastic Elastomers (TPEs)
Thermoplastic Elastomers, commonly known as TPEs, are a class of polymers that combine the elasticity of rubber with the processability of plastics. Unlike traditional vulcanised rubber, TPEs can be melted and reshaped multiple times, making them highly versatile and sustainable. They offer excellent flexibility, durability, and resistance to heat, chemicals, and abrasion — properties that are highly desirable in automobile components.
In the context of the automobile industry, TPEs serve as an ideal material for applications requiring comfort, flexibility, and safety while also contributing to weight reduction and environmental sustainability.
The Role of TPEs in the Indian Automobile Industry
India is one of the largest automobile markets globally, with a rapidly growing demand for passenger vehicles, commercial vehicles, and electric vehicles (EVs). To cater to this growth while aligning with government regulations on emissions and safety, the industry needs materials that enhance vehicle performance and sustainability. TPEs meet these criteria perfectly and are increasingly being integrated into automobile manufacturing in India.
1. Lightweight Components
Weight reduction is crucial for improving fuel efficiency and reducing carbon emissions in vehicles. TPEs, being lighter than traditional rubber and metals, help reduce the overall weight of automobile parts such as seals, gaskets, grips, and mats. This contributes to better mileage and lower emissions, supporting India’s commitment to environmental sustainability.
2. Better Comfort and Safety
TPEs are widely used in interior automobile parts like soft grips, armrests, and foot mats due to their soft touch and flexibility. These materials also provide excellent shock absorption, improving passenger comfort and vehicle safety during rides.
3. Durable and Weather-Resistant
The Indian climate presents challenges such as high temperatures, monsoons, and dust. TPEs exhibit excellent resistance to heat, UV radiation, and chemicals, making them ideal for external parts like seals and weatherstrips. Their durability ensures long-lasting performance even under harsh conditions, reducing maintenance costs for vehicle owners.
4. Electric Vehicle Applications
With India accelerating towards electric mobility, TPEs are increasingly vital in EV manufacturing. They provide insulation for electric wires and cables, flexible seals for battery compartments, and components for charging ports, enhancing the safety and reliability of electric vehicles.
Key Applications of TPEs in Indian Automobiles
DPL Group of Companies, as a leading manufacturer in India, produces high-quality TPEs specifically designed for various automobile applications. Here are some prominent uses:
Soft Grips and Handles
TPEs are used to manufacture tool grips and soft-touch handles that improve ergonomics for drivers and passengers. Their flexibility and durability make them ideal for steering wheel covers, gear knobs, and door handles.
Seals and Weatherstrips
Automobile doors, windows, and sunroofs require effective sealing against water, dust, and noise. TPE-based seals provide excellent elasticity and weather resistance, ensuring airtight and watertight closures.
Footwear and Floor Mats
Indian vehicles often use TPE-based floor mats and footwear inserts that are easy to clean, durable, and resistant to wear and tear. These mats contribute to maintaining vehicle hygiene, especially during monsoon seasons.
Electric Wire and Cable Insulation
TPEs manufactured by DPL Group of Companies are used for insulating electric wires and cables in vehicles. Their excellent electrical properties and heat resistance make them indispensable in automotive wiring harnesses.
EVA Slippers and Yoga Mats
Although slightly beyond traditional automobile parts, TPE technology also supports lifestyle products connected to automobile journeys such as comfortable EVA slippers and yoga mats for wellness-conscious drivers.
Advantages of Using TPEs in Indian Automobile Manufacturing
The shift towards TPEs in the automobile sector is driven by numerous benefits that these materials offer over traditional alternatives:
Cost Efficiency
TPEs allow for simplified manufacturing processes since they can be moulded and recycled, reducing production costs and waste. For Indian automobile manufacturers looking to balance quality and affordability, TPEs present an economically viable choice.
Environmental Sustainability
Recyclability of TPEs aligns with India’s environmental goals and policies promoting greener manufacturing. By using TPEs, manufacturers can reduce reliance on non-recyclable materials, minimise waste, and lower the carbon footprint of vehicles.
Versatility and Design Flexibility
The ease of moulding TPEs allows manufacturers to create complex designs and customised parts that enhance the functionality and aesthetics of vehicles. This flexibility supports innovation in vehicle interiors and exteriors, meeting diverse consumer preferences.
Improved Performance
TPEs provide superior resistance to abrasion, chemicals, and temperature extremes compared to traditional rubber. This translates into longer-lasting components and improved vehicle reliability, especially suited to India’s diverse terrain and climate.
Conclusion
Thermoplastic Elastomers are not just materials; they are catalysts for innovation in the Indian automobile industry. By combining flexibility, durability, and sustainability, TPEs enable manufacturers to build vehicles that meet modern standards of efficiency, safety, and comfort. With DPL Group of Companies’ commitment to quality and innovation, the Indian automobile sector is set to accelerate on the path of sustainable growth powered by the versatility of TPEs.